Quality is king in the Auto Industry
Quality is paramount. From safety to performance, consumers expect vehicles to meet high standards, making quality a top priority for manufacturers. Ensuring that every component meets rigorous specifications is essential for building trust and brand loyalty among customers. Quality defects not only pose risks to driver safety but can also damage a manufacturer's reputation and lead to costly recalls and warranty claims.
To maintain high levels of quality, automotive manufacturers implement stringent quality control measures throughout the production process. This includes conducting thorough inspections at every stage of manufacturing, from raw materials to final assembly. Additionally, advanced testing techniques such as computer-aided simulations and performance evaluations help identify potential defects early on, enabling manufacturers to address issues before they impact the final product.
With the rise of smart manufacturing technologies, such as IoT sensors and data analytics, automotive companies can now monitor quality in real-time and identify trends or anomalies that may indicate potential issues. By leveraging big data and predictive analytics, manufacturers can proactively address quality concerns, optimize processes, and continuously improve product quality. Ultimately, prioritizing quality not only enhances customer satisfaction but also ensures the long-term success and competitiveness of automotive companies in today's demanding marketplace.
What is a quality defect?
In the automotive industry, a quality defect refers to any deviation from the specified standards, requirements, or expectations regarding the design, manufacturing, or performance of automotive components, parts, or vehicles. These defects can manifest in various forms, including structural flaws, functional deficiencies, cosmetic imperfections, or safety hazards, and may result from errors or shortcomings in the design, manufacturing, assembly, or testing processes.
Quality defects can occur at any stage of the automotive production lifecycle, from the sourcing of raw materials and components to the final assembly of vehicles. Common examples of quality defects in the automotive industry include faulty welds, misaligned components, defective electrical systems, malfunctioning safety features, paint imperfections, and dimensional inaccuracies. These defects can compromise the reliability, durability, safety, and overall quality of vehicles, leading to customer dissatisfaction, warranty claims, recalls, and potential legal liabilities for automotive manufacturers.
Quality defects in the automotive industry requires rigorous quality control measures, comprehensive testing protocols, and continuous improvement initiatives throughout the supply chain and production process. Manufacturers employ various techniques and tools, such as statistical process control, failure mode and effects analysis, root cause analysis, and quality management systems like ISO 9001, to identify, prevent, detect, and correct quality defects before they reach customers. By prioritizing quality assurance and implementing robust quality management practices, automotive companies can uphold their reputation, meet regulatory requirements, and deliver safe, reliable, and high-quality vehicles to consumers.
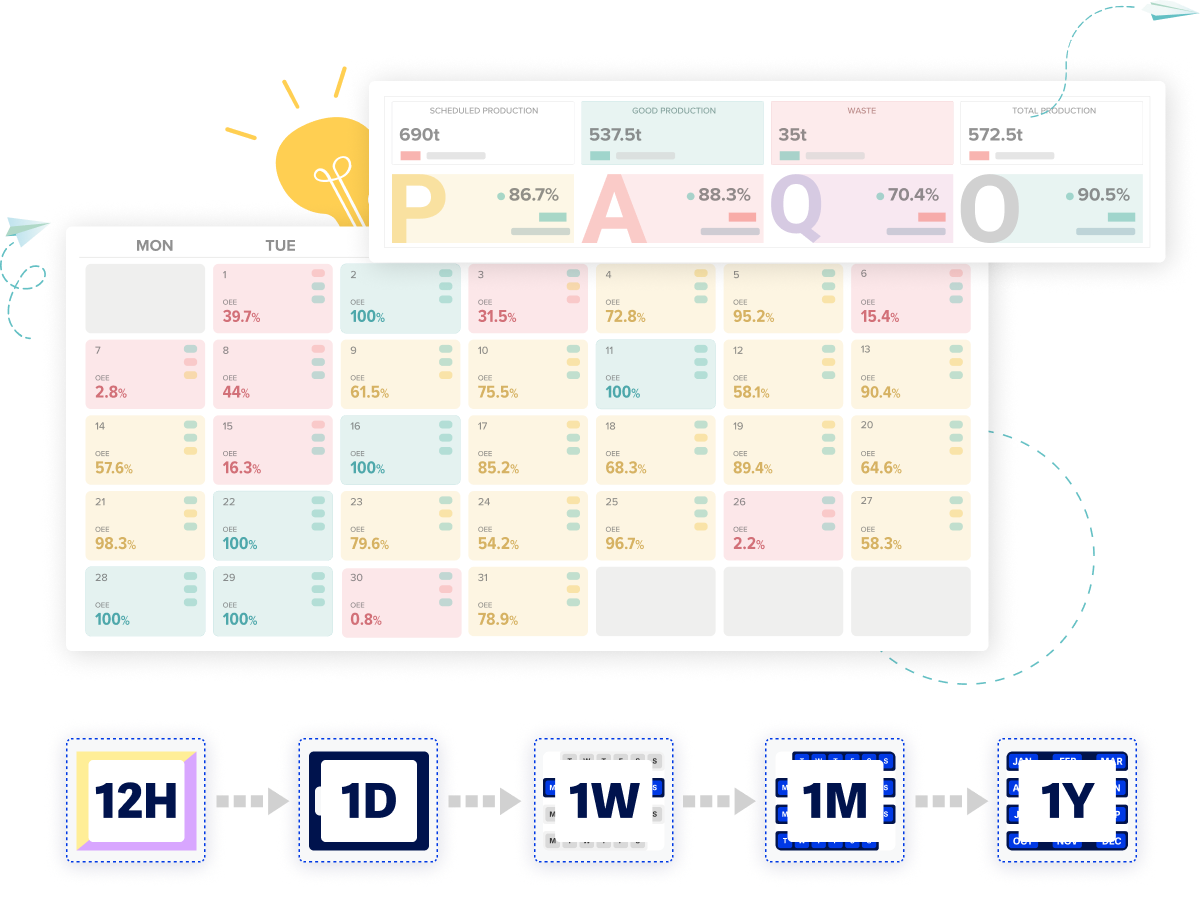
Data-Driven Decision with Smart Technology
The impact of quality defects on automotive manufacturing
Quality defects are a major problem in auto manufacturing. They can lead to poor customer satisfaction, higher costs, lost revenue and low morale. Quality defects can also damage a company's reputation and reduce market share--not to mention cost you money.
In order to prevent these problems from happening (and if they do happen), it's important that you know how best to track defects so that they can be fixed before they cause too much damage.
There are many ways to track defects. You can use a simple spreadsheet, or you can invest in software that will do all the work for you. There are also many different types of software that may be more appropriate depending on what kind of products you make and how large your company is.
If you are just starting out and only making a few products, then a simple spreadsheet will do the trick. You can create multiple columns for each type of defect that happens during production, such as scratches on car bodies or dented fenders, broken parts, or missing instructions.
MES solutions can help manufacturers identify and prevent quality defects
MES solutions can help manufacturers identify and prevent quality defects.
- MES solutions can help manufacturers monitor and control their production processes.
- MES solutions can take proactive steps to eliminate quality defects by identifying potential causes of those defects before they occur.
- By using an integrated system that monitors all aspects of your manufacturing process, you will be able to achieve higher efficiency while reducing waste and costs associated with rework or scrap materials.
- MES solutions can help you increase throughput, reduce labor costs and improve quality control.
- Using an MES system, you can configure the software to monitor and control equipment, production lines and processes.
- You can also use MES systems to monitor performance against set parameters or standards. Such systems automate many tasks that otherwise would require manual intervention by a human operator.
There are two main types of software:
There are primarily two categories: those tailored for companies specializing in a single product and those designed for enterprises producing multiple products. For companies focused on a single product, the software tends to be highly specialized and optimized to support the unique manufacturing processes and requirements associated with that particular product. These solutions often offer deep integration with the specific machinery, equipment, and workflows involved in producing the single product, enabling precise control and efficiency.
On the other hand, manufacturers producing multiple products require more versatile and flexible software solutions capable of accommodating diverse production lines, product variants, and customization options. These software platforms typically offer modular architectures and configurable features to adapt to different product specifications, production schedules, and quality standards. They also facilitate centralized management of resources, such as materials, equipment, and labor, across various product lines and manufacturing facilities.
Ultimately, the choice between these two types of software depends on the nature of the manufacturing operations and the strategic objectives of the company. While single-product software may offer focused functionality and upgraded processes for specialized production, multi-product software provides scalability, adaptability, and broader operational coverage to support complex and diversified manufacturing environments. Selecting the most suitable software solution entails evaluating factors such as product complexity, production volume, market demand, and long-term growth plans to ensure optimal alignment with the organization's objectives and requirements.
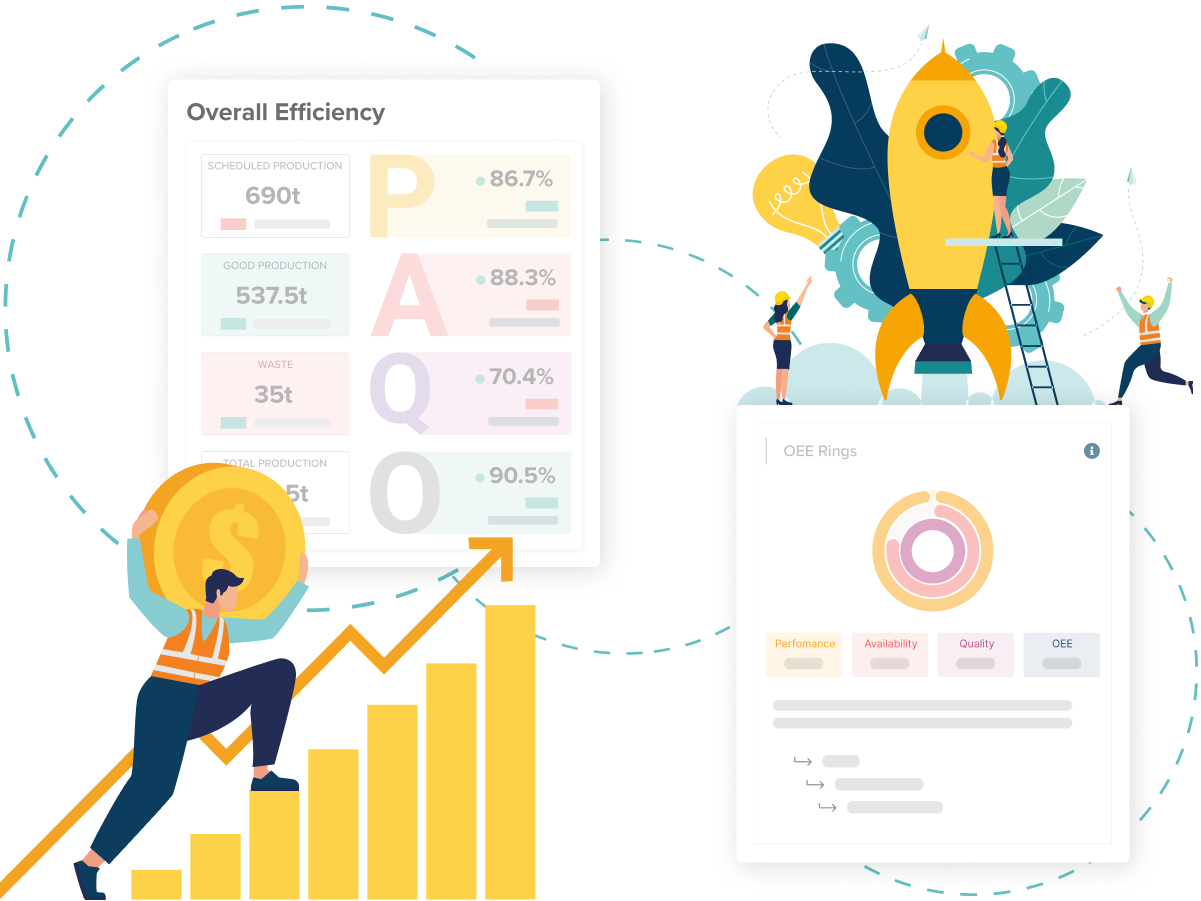
Increase production in Automotive Industry
Improve efficiency and quality, as well as gain a competitive edge in the industry
Implementing modern manufacturing execution systems (MES) and manufacturing operations management (MOM) solutions is essential for automotive manufacturers looking to enhance efficiency, quality, and competitiveness. These advanced technologies enable real-time monitoring, control, and optimization of production processes, leading to streamlined operations and improved resource utilization. By automating routine tasks, reducing manual errors, and minimizing downtime, MES and MOM solutions help manufacturers maximize productivity and throughput while maintaining high levels of product quality.
Additionally, modern MES and MOM platforms provide comprehensive data analytics capabilities, allowing automotive manufacturers to gain valuable insights into their operations. By analyzing key performance indicators (KPIs), identifying bottlenecks, and predicting maintenance needs, these systems empower decision-makers to make data-driven decisions that drive continuous improvement. This proactive approach to manufacturing management enables companies to respond quickly to changing market demands, optimize production schedules, and allocate resources more effectively, ultimately enhancing operational efficiency and profitability.
Adopting modern MES and MOM solutions allows automotive manufacturers to stay competitive in an increasingly dynamic and demanding industry landscape. By embracing digital transformation and leveraging cutting-edge technologies such as artificial intelligence (AI) and machine learning (ML), companies can differentiate themselves by offering innovative products, delivering superior customer experiences, and achieving operational excellence. With MES and MOM solutions as foundational pillars of their digital strategy, automotive manufacturers can position themselves for long-term success and thrive in a rapidly evolving marketplace.
Conclusion
It is clear that the auto industry is constantly changing and evolving. This makes it even more important for manufacturers to stay on top of their game by using technology such as MES systems to improve efficiency and quality across their manufacturing process.